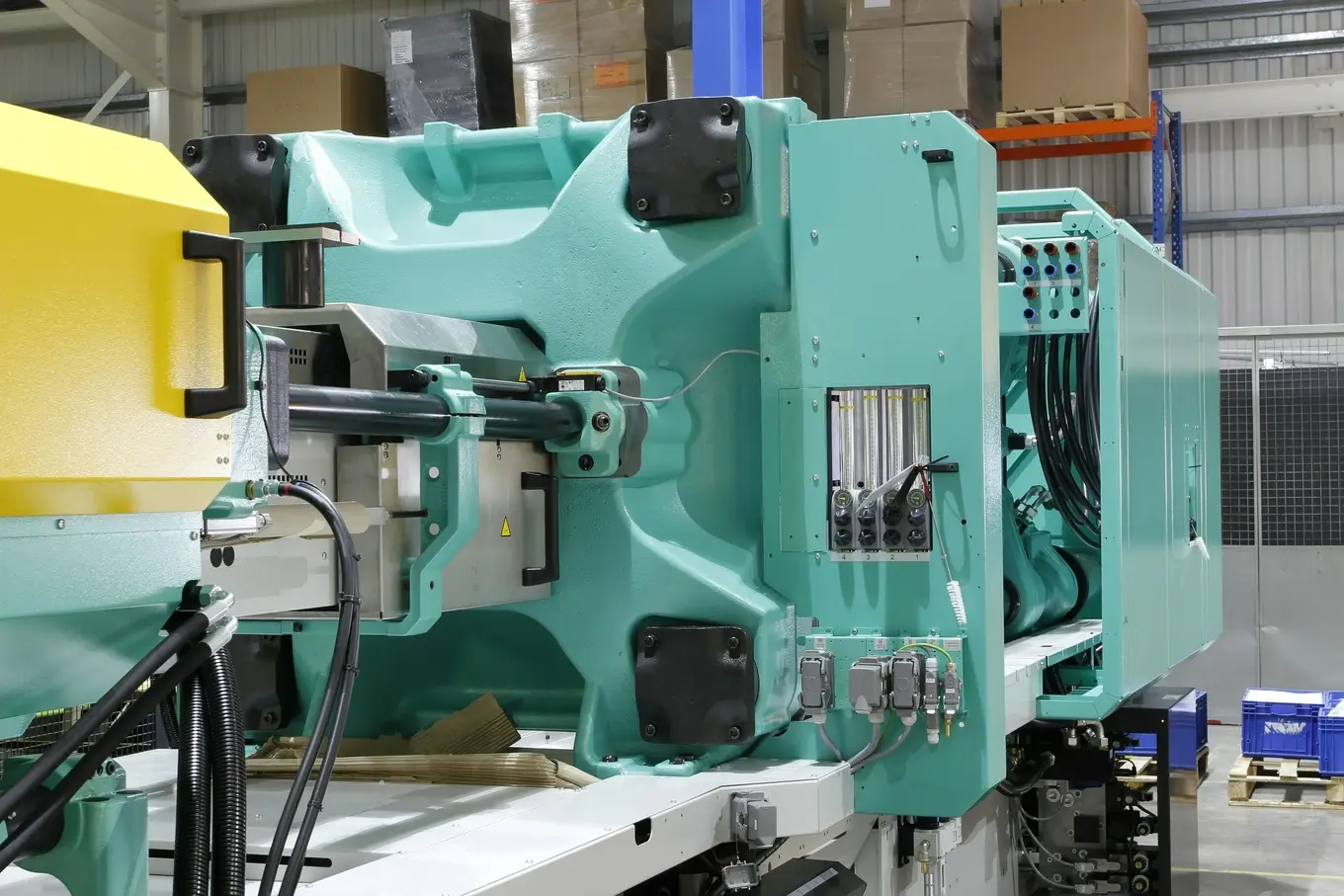
05 cze Jak przebiega produkcja metodą wtrysku?
Produkcja elementów z tworzyw sztucznych metodą wtrysku to powszechnie stosowany proces w wielu branżach, m.in. motoryzacyjnej, elektronicznej czy opakowaniowej. Polega on na formowaniu detali z granulatu polimerowego pod wpływem wysokiej temperatury i ciśnienia. Materiał zostaje uplastyczniony, a następnie wtryskiwany do formy, gdzie przyjmuje docelowy kształt. Cały proces odbywa się w specjalistycznych maszynach zwanych wtryskarkami. Dzięki tej technologii możliwa jest produkcja dużych serii identycznych wyrobów w krótkim czasie, co przekłada się na efektywność i powtarzalność wykonania. Produkcja metodą wtrysku jest dostępna w ofercie firmy Rekpol. Przyjrzyjmy się temu bliżej.
Etapy procesu wtrysku tworzywa
Proces rozpoczyna się od zasypania leja wtryskarki granulatem tworzywa, który następnie trafia do cylindra grzewczego. Tam materiał zostaje rozgrzany do odpowiedniej temperatury, co prowadzi do jego stopienia i uzyskania jednorodnej masy. Kolejnym krokiem jest przemieszczanie uplastycznionego tworzywa za pomocą ślimaka w kierunku dyszy, skąd zostaje wstrzyknięte do wnęki formy. Wewnątrz formy następuje szybkie schłodzenie i zestalenie tworzywa, co pozwala uzyskać oczekiwany kształt detalu. Po zakończeniu cyklu forma się otwiera, a gotowy produkt zostaje wypchnięty przez układ wypychający. Każdy etap musi być precyzyjnie kontrolowany, ponieważ od właściwego ustawienia parametrów zależy jakość końcowego wyrobu.
Znaczenie formy i parametrów produkcji
Formy wtryskowe odgrywają kluczową rolę w całym procesie, ponieważ to one nadają kształt produkowanym elementom. Muszą być wykonane z dużą dokładnością, często z hartowanej stali lub innych odpornych materiałów. W zależności od złożoności detalu formy mogą być jedno- lub wielogniazdowe, wyposażone w systemy chłodzenia, prowadnice oraz mechanizmy wypychające. Istotne są również parametry technologiczne takie jak ciśnienie wtrysku, temperatura cylindra, prędkość ślimaka czy czas chłodzenia. Każdy z nich wpływa na strukturę tworzywa, dokładność wymiarową oraz ewentualne wady wypraski. Odpowiednia konfiguracja maszyn pozwala zoptymalizować cały cykl i uzyskać trwałe, estetyczne komponenty gotowe do dalszego wykorzystania.
Sorry, the comment form is closed at this time.